What Are the Advantages of Automated Guided Carts in Warehouses?
Automated guided vehicles (AGVs) and automated guided carts (AGCs) are highly advanced technologies that have transformed the warehousing industry. There are several benefits associated, including lower costs and increased fulfilment efficiency, since they eliminate the need for wire-guided forklifts and pallet jacks to transfer goods manually. So, using AGV system design, warehouses can operate more efficiently, safely, and reliably. It leads to improved productivity, lower operational costs, and increased customer satisfaction.
With their ability to transport goods precisely and efficiently, these automated vehicles have become indispensable to modern warehousing operations. Increasingly, as e-commerce, manufacturing, and logistics demand cutting-edge technologies, businesses are turning to cutting-edge technologies. One such innovation is the use of Automated Guided Carts (AGCs). AGCs are called Automated Guided Vehicles (AGVs) or Autonomous Mobile Robots (AMRs). These are significant components in the evolution of automated material handling systems.
Automated Guided Carts (AGCs) can navigate a specific path without human assistance. They are equipped with sensors that enable them to detect obstacles and avoid crashes, which makes them safer than automated forklifts commonly used in warehouses and fulfilment centres. These robotic solutions can be used in a variety of applications. It includes manufacturing, support picking operations in distribution settings, material storage, and transportation. This article explores the concept of AGCs, their advantages, types, costs, applications, and features, shedding light on their transformative impact on warehouse operations.
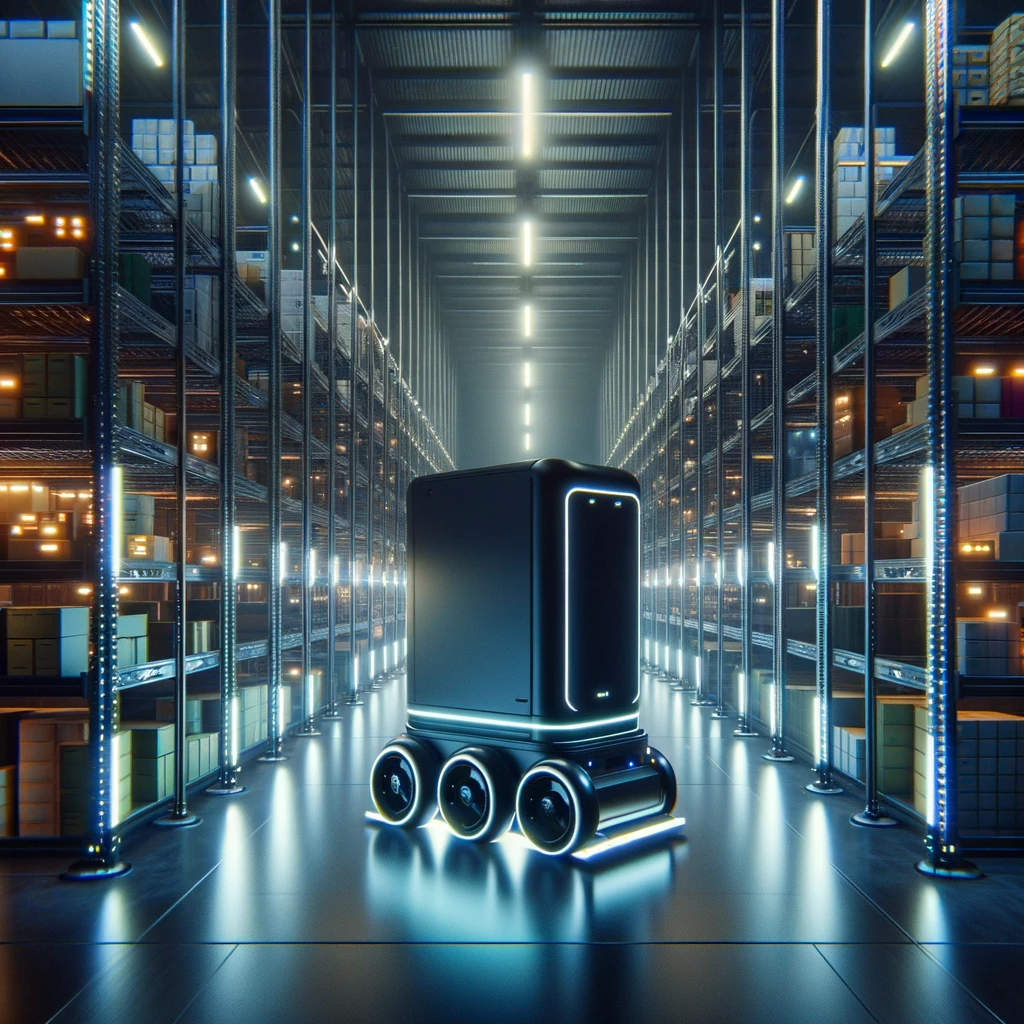
What are the Automatic Guided Carts (AGCs)
Automated guided carts are mobile robots built with a small structure and low profile. They’re designed to move carts or shelves underneath them and can be used for various purposes. Depending on how AGCs navigate, they can be classified as either Automated Guided Vehicles (AGV) if they follow lines (like magnetic navigation) or Autonomous Mobile Robots (AMR) if they use natural navigation methods.
Automated Guided Carts (AGCs) usually have a capacity of 0.5 tons, approximately 1,100 pounds. However, some vehicles can carry up to 3 tons or 6,600 pounds and more. Typically, the maximum speed of AGCs is around 40 meters per minute or 130 feet per minute, equivalent to 1570 inches per minute. However, AGCs with line following navigation (assembly line AGVs) can attain a maximum speed of 60 meters or 195 feet per minute. AGCs with natural navigation (AMRs) can run up to 120 meters or 390 feet per minute. The height of the AGC is a crucial factor, as it must be able to go under a cart or a shelf. Low-profile AGCs are more versatile and require fewer modifications to carts.
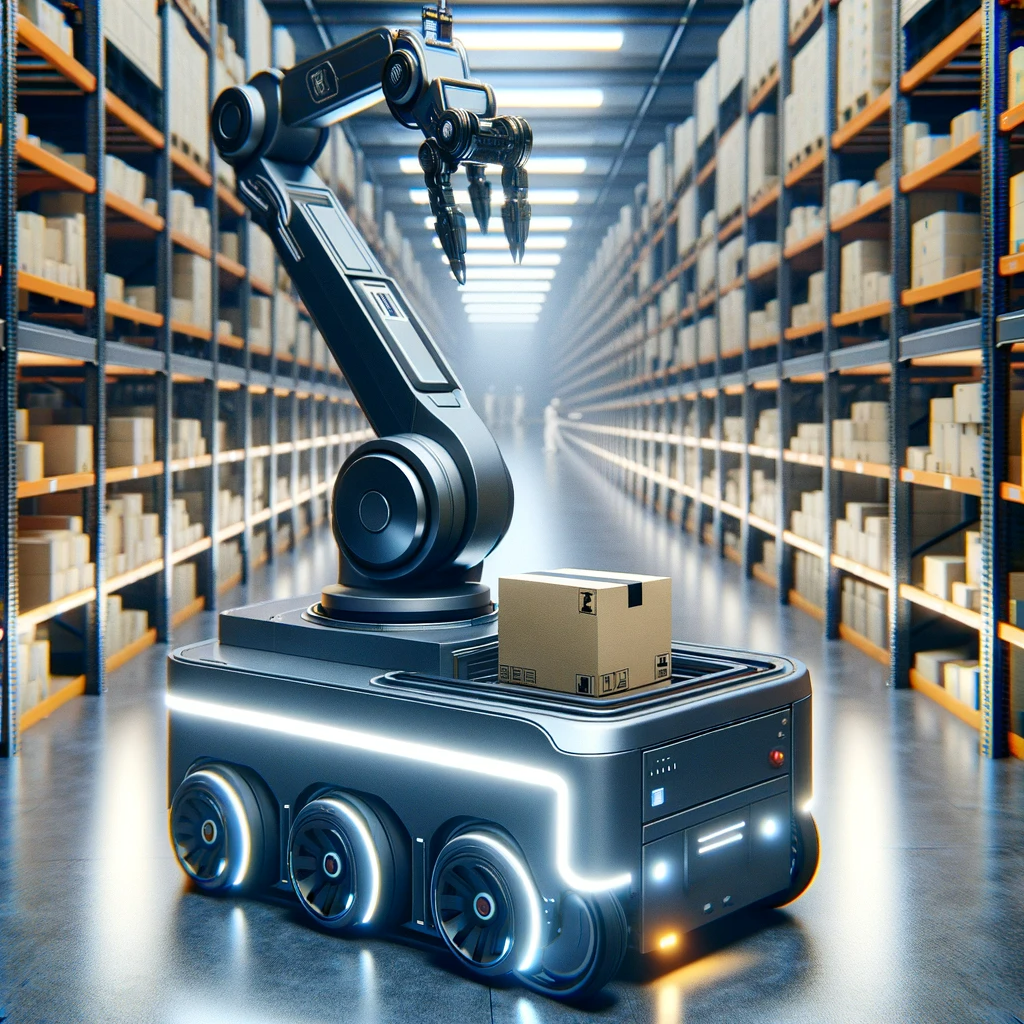
Advantages of Automated Guided Carts (AGCs) in Warehouse
Integrating Automated Guided Carts (AGCs) into warehouse operations offers several advantages beyond basic automation. These benefits address immediate operational needs and contribute to long-term sustainability and competitiveness in the ever-evolving business landscape.
1. Increased Efficiency
AGCs significantly boost operational efficiency by streamlining material handling processes. Automated Guided Carts (AGCs) can tirelessly operate without needing shifts or breaks, unlike human workers who are limited by physical constraints. This unparalleled ability ensures an uninterrupted and consistent flow of goods, essential for businesses that always require efficiency and productivity. The use of AGCs also reduces the need for human intervention, which means fewer errors and increased safety in the workplace. This continual operation translates into higher throughput. Hence, it reduces lead times and improves overall supply chain responsiveness.
2. Precision and Accuracy
Automated Guided Carts (AGCs) are equipped with advanced navigation systems that ensure every item is transported with unparalleled precision and accuracy. In the complex warehouse environment, AGCs keep track of their location and the location of all items while navigating through narrow aisles and avoiding obstacles. This level of accuracy is essential for maintaining an organized and efficient warehouse layout. It helps minimize the risk of inventory placement errors and enhances order fulfilment accuracy. Thus, improved accuracy, in turn, leads to higher customer satisfaction and loyalty.
3. Safety
Safety is a foremost concern in any warehouse environment. AGCs have advanced safety features, such as accident detection and avoidance systems. These technologies mitigate the risk of accidents. It helps in protecting both the AGCs and the human workforce. Therefore, implementing AGCs also reduces the need for manual material handling tasks. It minimizes the potential for workplace injuries.
4. Flexibility
AGCs offer a level of flexibility that is significant in dynamic warehouse environments. The adaptability of these systems makes it effortless to make changes to warehouse layouts, product lines, or operational processes. These changes can be made quickly and efficiently, allowing the system to keep up with the changing needs of the business. The reconfiguration process is specific and can be done without disrupting the daily operations of the warehouse. The flexibility of these systems ensures that they can adapt to any future changes, making them a valuable investment for any business. This flexibility is particularly advantageous for businesses experiencing growth or those adapting to seasonal fluctuations in demand.
5. Cost Savings
While the initial investment in AGCs may seem substantial, the long-term cost savings are compelling. There is a reduction in labour costs as manual tasks are automated. It contributes significantly to the overall cost-effectiveness of AGC implementation. Additionally, the improved energy efficiency and minimized errors result in savings related to damaged goods, rework, and other operational inefficiencies.
6. Enhanced Workforce Productivity
By automating routine and physically demanding tasks, AGCs allow human workers to focus on more value-added activities. It includes complex decision-making, problem-solving, and managing exceptions. It enhances overall workforce productivity and job satisfaction, as employees can contribute their skills to tasks that require a human touch.
7. Scalability
Automated Guided Carts (AGCs) are an innovative solution for businesses that require a scalable and adaptable approach to their material handling needs. AGCs are designed to operate autonomously, eliminating the need for human intervention and increasing efficiency, safety, and productivity. As the volume of goods to be handled increases, additional AGCs can be easily integrated into the system. This scalability ensures warehouse operations can seamlessly adapt to changing business conditions without significant disruptions.
8. Data Driven Decision Making
AGCs are often equipped with sensors and data collection capabilities. This real-time data on material movement, operational efficiency, and performance metrics empowers warehouse managers to make informed decisions. Analysing this data can lead to continuous process improvement. Thus, it optimizes the overall warehouse operation.
Therefore, the advantages of incorporating Automated Guided Carts into warehouse operations extend well beyond mere automation. These systems enhance efficiency, accuracy, and safety. It contributes to a more productive and cost-effective warehouse environment. As businesses strive to stay competitive and responsive to market demands, adopting AGCs emerges as a strategic move toward achieving operational excellence in logistics and supply chain management.
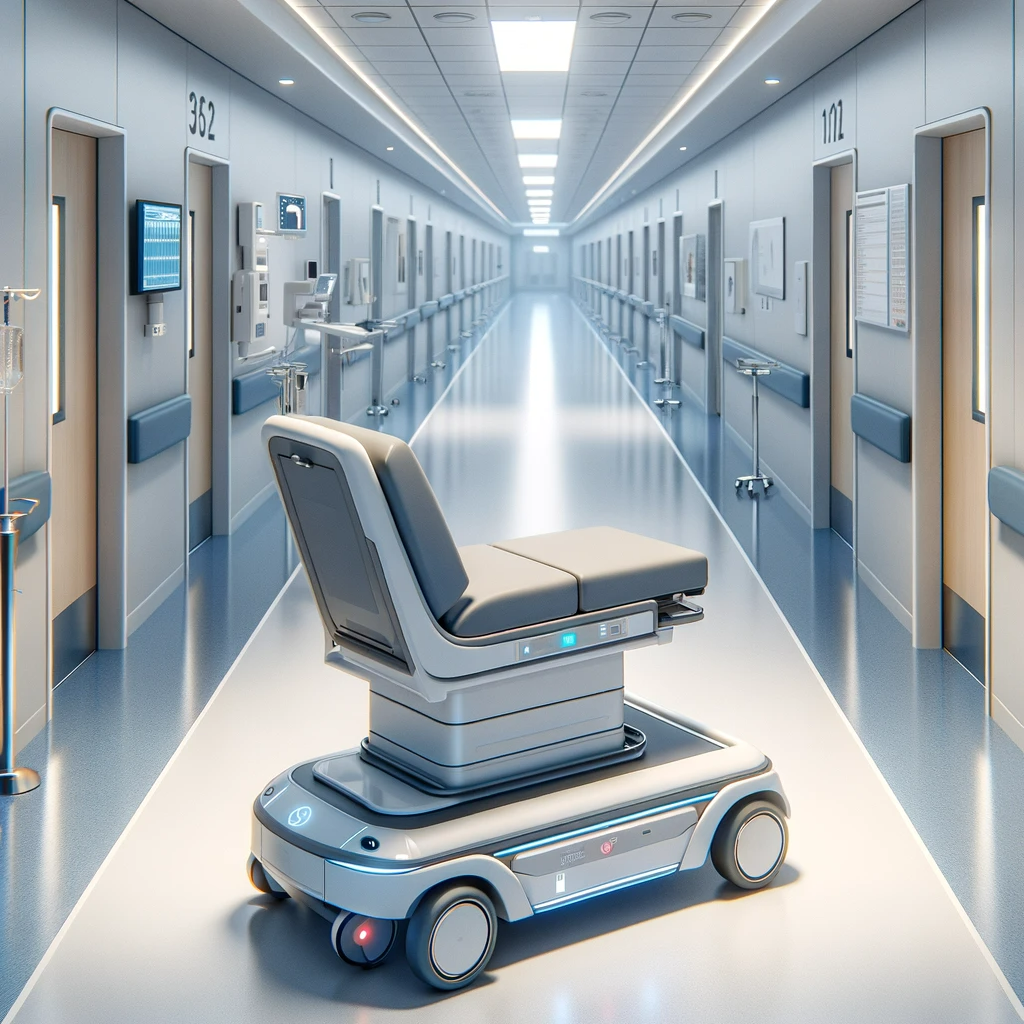
Main Applications of Automatic Guided Carts:
Automated Guided Carts (AGCs) encounter diverse applications across various industries due to their versatility and adaptability. These autonomous rail-guided vehicles are designed to handle material transport efficiently, and their main applications in warehouses and industrial settings include the following.
Healthcare and Hospitals
AGCs are employed for the automated transport of medical supplies, equipment, and even patient records within hospital facilities. This application enhances the efficiency of healthcare operations by ensuring timely and precise delivery of essential items. It also contributes to the overall patient care process. Moreover, in healthcare settings, AGCs help in transport medications, medical supplies, and other pharmaceutical items within hospital pharmacies. This application simplifies the logistics of managing and distributing medications. It also contributes to accurate prescription fulfilment and minimizing delays. AGCs play a role in automating the movement of linens, medical waste, and other materials within hospitals. It ensures a hygienic and efficient process for managing linens, disposing of waste, and maintaining a clean and organized healthcare environment.
E-commerce and Warehousing
AGCs are extensively used for order fulfilment processes in e-commerce and warehouse settings. These carts autonomously transport items from storage locations to packing stations. It helps in optimizing the picking and packing operations. This application contributes to faster order processing and improved accuracy in shipment preparation. AGCs transport goods within warehouses, distribution centers, and fulfilment centres. They navigate through lanes, carrying products from one location to another. Thereby, these carts streamline the overall logistics and reduce the manual effort required for material handling. AGCs contribute to efficient inventory management by automating the movement of goods in and out of storage locations. This application ensures real-time tracking of inventory levels. Hence, it minimizes errors and discrepancies and enhances the accuracy of stock control.
Industry Applications
In manufacturing, AGCs are utilized for the movement of raw materials, work-in-progress components, and finished goods within the production facility. This application optimizes the material flow, supporting efficient manufacturing processes and reducing the reliance on manual handling.
AGCs play a significant role in supporting assembly line operations by transporting components between workstations. This application contributes to the smooth and continuous flow of materials during the manufacturing process. It also helps in enhancing overall production efficiency. AGCs are customized for specific industry applications to address unique challenges. It includes tasks such as transporting specialized equipment, managing heavy loads, or navigating through environments with specific safety requirements.
Thus, in each of these sectors, AGCs are a transformative technology that enhances operational efficiency, reduces manual labour, and contributes to the overall improvement of processes. The versatility of AGCs allows them to be adapted to the specific needs of different industries. And it makes them a valuable asset in the evolving landscape of automation.
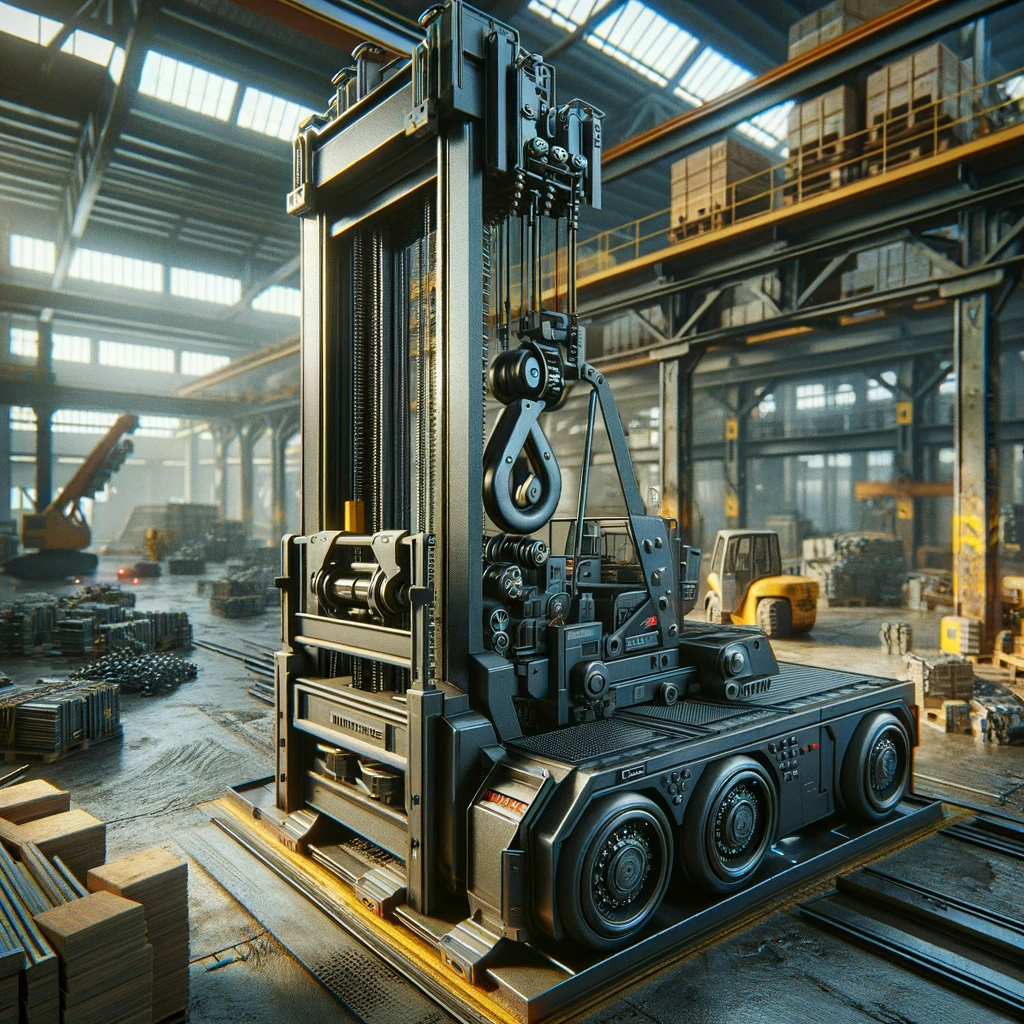
Types of Automated Guided Carts AGCs
Although there is no official classification for AGCs, we could distinguish them depending on how they engage the load.
Pin hook AGCs
This particular AGC (Automated Guided Cart) uses pin hooks, which can either be a single hook or a pair of hooks, to attach to a cart. It is necessary to have a platform, trolley, or cart equipped with wheels that are consistent with the AGC’s hook and shape to ensure compatibility of the cart. Once the AGC has successfully hooked onto the load, it will then pull it while the wheels of the cart will support the weight of the load. For better cart mobility, it is recommended to have all swivel wheels in the cart. This type of AGV solution is the most cost-effective because it uses magnetic or optical line navigation, which is the most specific navigation technology. Since the load is supported by the cart, the AGV cart structure and motorization are lighter, which allows for reasonable towing rates with limited power.
Lifting Devices and AGCs
In this instance, a mobile robot is capable of lifting all kinds of loads, including pallets, shelves, carts, boxes, and more. The best part is that the load doesn’t even need to have wheels, as the AGV cart can support the weight themselves. These robots are super smart and can navigate on their own without needing specific instructions to follow a particular path. They are known as autonomous auto-guide mobile robots, and they’re becoming more and more popular in different applications. For instance, they’re widely used in warehouses as autonomous mobile robots for goods-to-person applications, which makes the work of the pickers much easier and more efficient.
Features of AGCs
- Navigation Systems: AGCs use various navigation systems. It includes laser guidance, magnetic strips, or vision-based systems to navigate through the warehouse environment.
- Sensors and Safety Features: Equipped with sensors, AGCs can detect obstacles, people, or other rail-guided vehicles in their way. It ensures safe and efficient operations.
- Integration with Warehouse Management Systems (WMS): AGCs are often integrated with WMS to optimize route planning, task prioritization, and overall warehouse operations.
- Remote Monitoring and Control: Many AGCs allow for remote monitoring and control. It helps in enabling operators to oversee operations and intervene if necessary.
Conclusion
Automated Guided Carts (AGCs) and Automated Guided Vehicles (AGVs) represent a significant shift in warehouse management. With their advanced technology, AGCs can transport materials and products with precision, speed, and safety, significantly improving warehouse efficiency and productivity.
AGCs are designed to operate without human intervention, reducing the risk of workplace accidents and minimizing labour costs. Overall, AGCs represent a game-changing solution for modern warehouse management. While the initial investment might be a consideration, the long-term benefits, including cost savings and improved operational performance, make AGCs a strategic choice for modern warehouses. As technology continues to advance, AGCs are expected to play an even more significant role in shaping the future of material handling in warehouses and distribution centres.