How Much Does an Automated Guided Vehicle Cost?
Automated Guided Vehicles (AGVs) have become integral in modern industrial settings. It offers a transformative solution to material handling challenges. The invention of AGVs signifies a major shift in material handling. It promises a revolution in operational efficiency. These self-guided robotic vehicles navigate through manufacturing plants, warehouses, and distribution centres. Thus, AGVs perform tasks that once relied heavily on manual labor.
While the benefits of AGVs are undeniable. It is significant to understand the financial aspects associated with their adoption. Businesses need to make informed decisions aligning with their operational and financial goals. As organizations increasingly turn to AGVs for enhanced and real-time efficiency and streamlined operations, understanding the details of costs associated with AGV robots becomes crucial. It is important to note that AGVs offer an effective return on investment by contributing to increased operational efficiency, cost savings, enhanced safety, and adaptability to changing production needs. In that regard, this guide will delve into the following topics.
- How much does an automated guided vehicle cost to buy?
- Types of AGV robot
- AGV automatic navigation
- How much does it cost to set up and install an AGV?
- Advantages of automated guided vehicles
So, read on to know more.
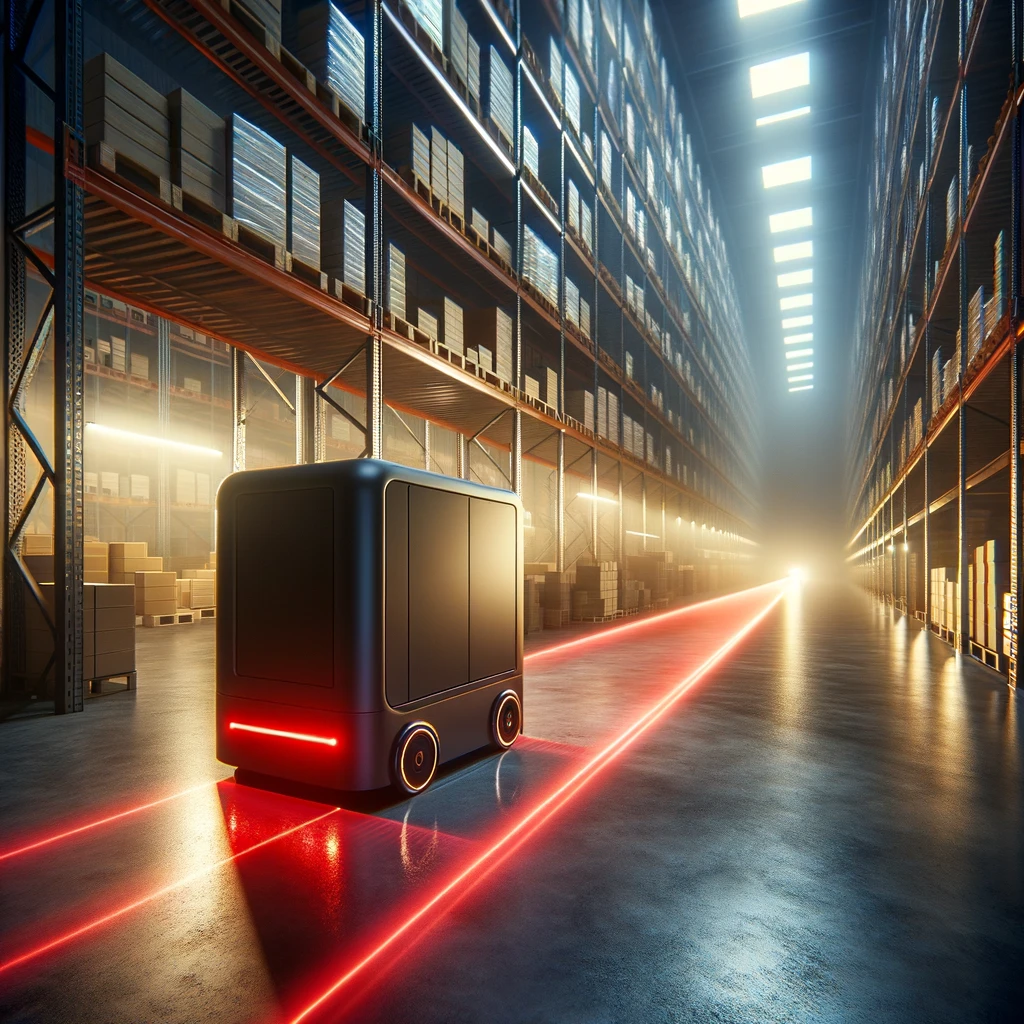
How Much Does an Automated Guided Vehicle Cost to Buy?
It is important to note that many factors can affect the price of AGVs. These might include aspects like how complex your use case is, what kind of navigation you need, and how heavy the loads that your AGVs will be carrying. So, if you’re thinking of investing in AGVs for your facility, there are some important things to consider that can impact the cost. For example, you’ll want to consider how many vehicles you need, what kind of AGV is best for your needs, how complicated the installation process will be, and what size your vehicles need. All of these factors can affect the cost of your AGV robot installation. So, it’s vital to think them through carefully. Remember, the price of your AGVs will ultimately depend on the size and volume of vehicles you require.
Automated Guided Vehicles (AGVs) vary in pricing depending on the primary product type. It includes Unit Load Vehicles, AGV Forklifts, and Towing/Tuggers. This pricing typically comes within the $40,000 to $200,000 range, considering factors such as size, vehicle type, load capacity, and navigational system. For AGV Forklifts, the estimated cost varies between $75,000 and $200,000. This range is decided by factors such as the product type and project specifications. It includes weight, load, and complexity. However, considerations like the AGV’s ability to operate in smaller spaces can impact the final cost.
In addition, Unit Load Vehicles, also called AGCs, are estimated to cost around $40,000. The diverse range of these vehicles introduces variability in pricing with key factors. It includes load and transport capacity and the type of navigation system installed. For instance, the cost can significantly differ based on the vehicle’s capability to transport loads ranging from 500kg to 2 tons. Automated Towing/Tugger Vehicles fall within the price range of $50,000 to $85,000. The specific cost depends on factors like the navigation system. These considerations reflect the automation and technological complexity level integrated into the Towing/Tugger Vehicles. It impacts the overall pricing structure.
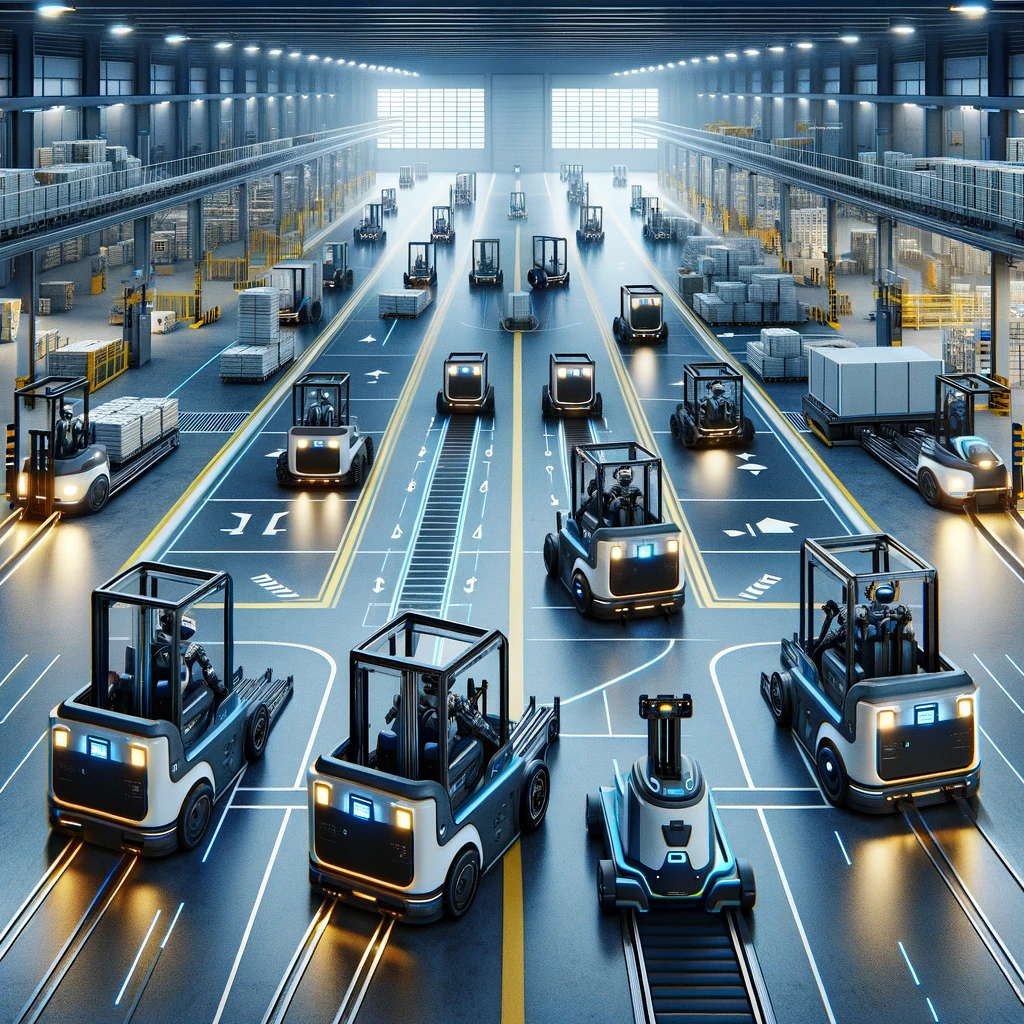
Types of AGV Robot
Automated Guided Vehicles (AGVs) come in various types. Each type is designed for specific material handling tasks within industrial and logistical settings. AGV type depends on the nature of the materials being transported, the layout of the facility, and the specific operational requirements. Here are some common types of AGVs.
1. Towing/Tugger Vehicles
Towing vehicles are made specifically for towing carts loaded with materials. It makes them suitable for material transport within manufacturing and distribution settings. Their design is suited to the efficient movement of bulk materials. Hence, tuggers contribute to optimized logistics workflows.
2. Unit Load Vehicles
This AGV robot handles individual items or loads, making it ideal for load handling and order-picking tasks. Their versatility extends to various applications. It allows businesses to adapt these AGVs to their specific material handling needs.
3. Forklift AGVs
Forklift AGVs are similar to the functionality of traditional forklifts, specializing in handling packages and heavy loads. It is widely used in warehouses and manufacturing plants. These AGVs offer a seamless transition from manual to automated material handling processes.
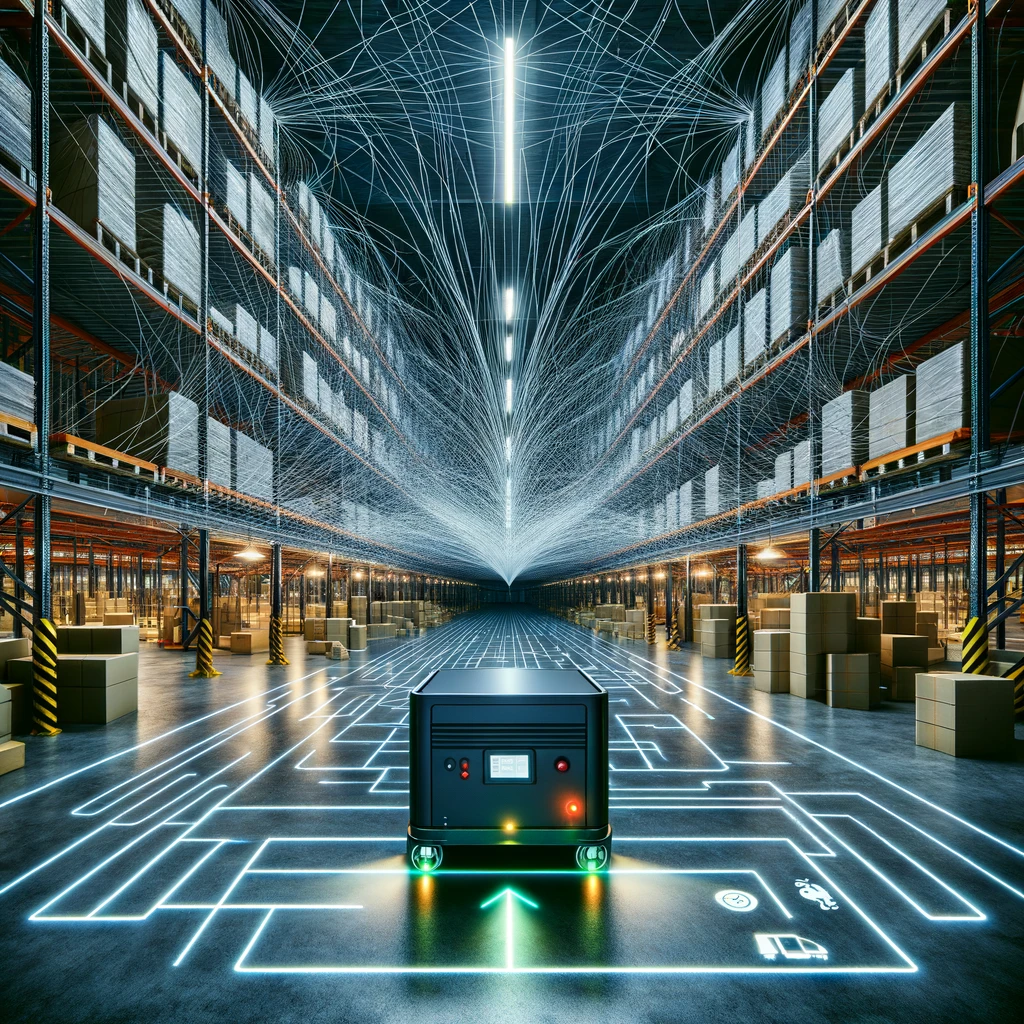
AGV Automatic Navigation
The ability of automated guided vehicles (AGVs) to navigate autonomously within industrial environments is largely a result of their automatic navigation systems. The efficiency and reliability of an AGV robot heavily depend on the navigation system, and various technologies are used to facilitate exact and seamless movement. Let’s explore the complex process of AGV automatic navigation.
1. Wire Guidance
In wire guidance, automatic guided vehicles follow an embedded wire or magnetic tape on the facility floor to determine where they need to go. AGV can detect a signal emitted by a wire to navigate itself. It is called wire guidance, and it’s known for its accuracy and reliability. It’s particularly helpful in manufacturing environments where a consistent and fixed way is necessary for efficient material transport.
2. Laser Guidance
Laser-guided navigation in AGVs uses lasers to scan the environment and create a real-time map. The AGV then navigates based on this map, adjusting its route to avoid obstacles. Laser guidance offers flexibility and adaptability. AGVs with laser navigation can operate in busy environments where layouts may change, and obstacles can appear unexpectedly.
3. Vision Based Systems
Vision-based navigation relies on cameras and sensors installed on the AGV to monitor its surroundings. The system processes visual data to detect obstacles, recognize paths, and make real-time automatic navigation decisions. Vision-based systems are suitable for environments with frequently changing layouts. They provide AGVs with a level of adaptability and responsiveness to occupied conditions.
4. Magnetic Guidance
Magnetic guidance involves the installation of magnetic markers on the floor. It creates a path for AGVs to follow. The AGV’s onboard magnetic sensors detect these markers, enabling accurate navigation. Magnetic guidance provides a reliable and cost-effective solution for AGV navigation. It is especially best for environments where other guidance methods may not be suitable.
5. Natural Features Navigation
AGVs using natural features navigation depend on recognizing distinctive features in the environment. It can be walls, columns, or landmarks. These features work as reference points for navigation. This method is versatile and effective in environments with limited infrastructure modifications.
Thus, the AGV automatic navigation system depends on factors such as the specific application, the nature of the working environment, and the level of flexibility required. Each navigation method has its advantages and considerations. So, businesses must carefully assess their operational needs to select the most suitable solution.
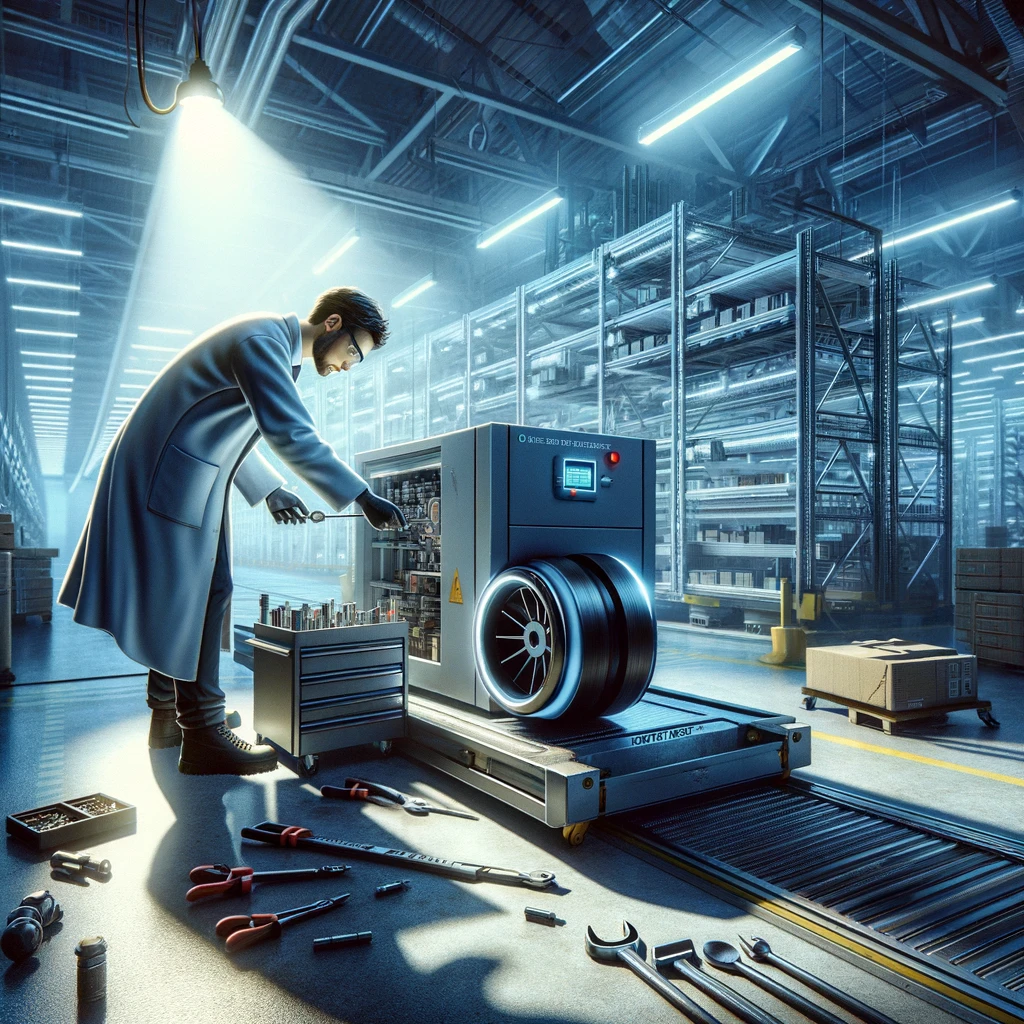
How Much Does It Cost to Set Up and Install an AGV?
The cost of setting up and installing Automated Guided Vehicles (AGVs) involves various factors. And it is a critical aspect to consider when planning to adopt these robotic systems. An AGV installation involves several elements contributing to the overall cost over and above the machine’s purchase price. Here’s a breakdown of the key concerns affecting the cost of setting up and installing AGVs.
Infrastructure Modification
AGVs often require modifications to the existing infrastructure to facilitate their operation. It includes installing guiding systems such as magnetic strips, wires, or markers on the floor to guide the AGVs along their designated paths.
Cost Impact: Modifying the infrastructure depends on the complexity of the facility layout, the type of guidance system, and the extent of modifications needed. More complex modifications may result in higher costs.
Integration with Existing Systems
AGVs must seamlessly integrate with existing systems, such as Warehouse Management Systems (WMS) and other automation systems. This integration ensures smooth workflow and efficient communication between different automated system components.
Cost Impact: The complexity of integration can influence costs. Customizing AGVs to communicate effectively with existing systems and ensuring accuracy may require additional programming and integration efforts.
Training and Support
Workforce training is a compulsory component of AGV implementation. The individuals responsible for operating, monitoring, and maintaining the AGVs must be trained to ensure efficient and safe operation. Additionally, ongoing support and maintenance agreements are often necessary to address issues promptly.
Cost Impact: Training programs, documentation, and ongoing support contracts contribute to the overall cost. Well-trained workers are essential for maximizing the benefits of AGVs and minimizing downtime due to operational issues.
Safety Measures
Implementing safety measures is foremost when introducing AGVs into a facility. It may involve installing additional safety features such as sensors, cameras, or signalling devices to prevent accidents and ensure the safety of both AGVs and human workers.
Cost Impact: The cost of safety measures depends on the complexity of the safety systems implemented. Advanced safety features may cost more but contribute to a safer working environment.
Customization and Configuration
Customizing AGVs to meet specific operational requirements and configuring them for optimal performance can involve additional setup costs. It may include adjusting AGV parameters, programming specific routes, and configuring load-handling mechanisms.
Cost Impact: The extent of customization and configuration required will influence costs. Sometimes, AGVs may need to be customized to meet specific operational needs.
Testing and Validation
AGVs undergo testing and validation after installation to ensure they operate according to specifications and safety standards. This phase includes fine-tuning navigation. It checks communication protocols and validates the overall functionality of the AGVs.
Cost Impact: Testing and validation are essential steps that may involve additional labor costs and potential adjustments to ensure the seamless operation of AGVs.
Therefore, the total cost to set up and install AGVs is the sum of these factors. In that way, businesses must carefully assess their specific requirements and operational environment. Investing in professional consultation and partnering with experienced AGV suppliers can help businesses navigate the complexities of installation. It will ensure a successful integration of AGVs into their operations.
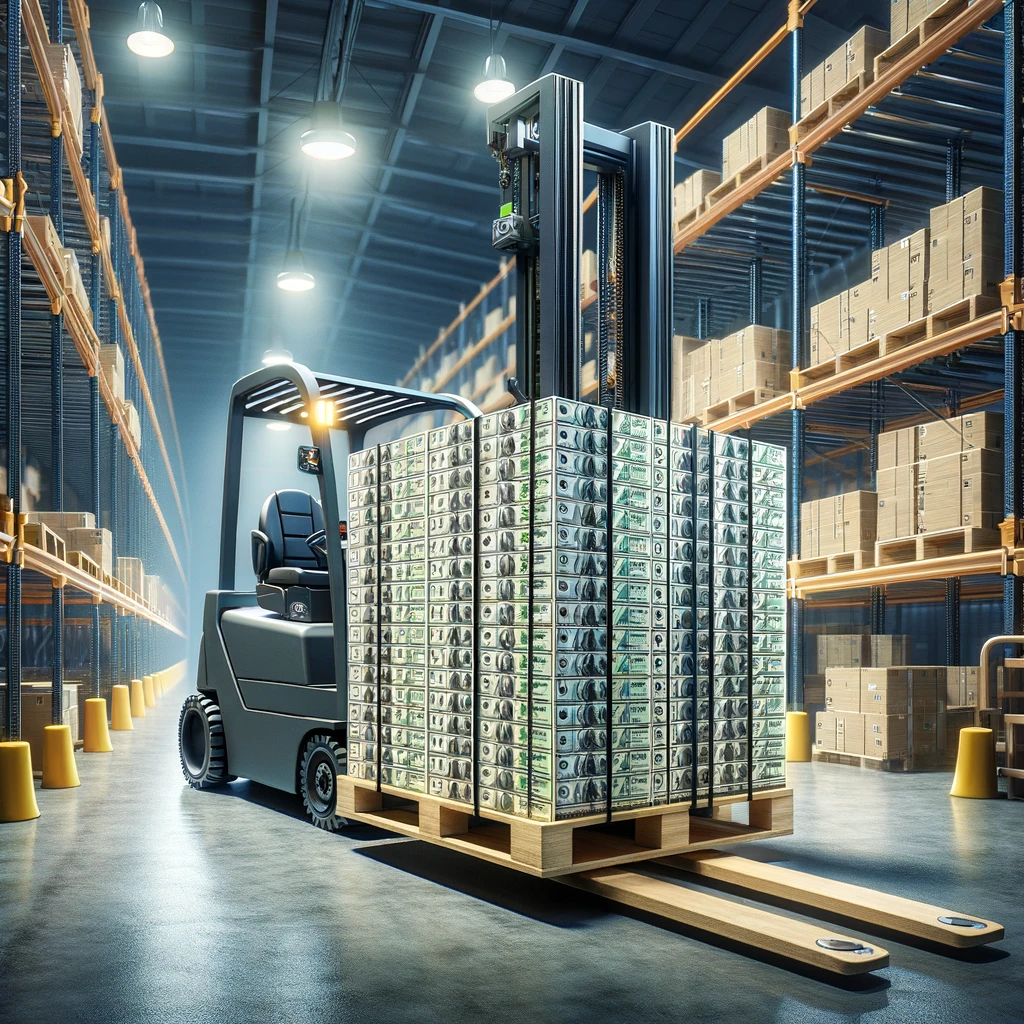
Advantages Of Automated Guided Vehicles
AGVs offer several advantages that justify investing in such robotic systems. For businesses looking to optimize their operations, AGVs are a strategic investment that goes beyond the initial purchase cost. Here are some of the advantages of AGVs.
- Increased Efficiency: AGVs operate around the clock. It optimizes material handling processes by reducing waiting time and ensuring a continuous and efficient flow of materials. Its boosted efficiency solves increased productivity and reduces operational tie-ups.
- Cost Savings: Adopting AGVs decreases labor costs as these robots handle repetitive tasks that would otherwise require human help. Moreover, the enhanced accuracy in material movement reduces errors and minimizes the associated costs of rework.
- Safety: AGVs come with advanced safety features, minimizing the risk of accidents in industrial settings. Integrating sensors and accident-avoidance systems ensures a safer work environment for AGVs and human personnel.
The Bottom Line
While the initial investment in AGVs may seem expensive, the long-term benefits make them a worthwhile consideration for businesses aiming to stay competitive in industrial automation. Automated Guided Vehicles (AGVs) can be a great way to save costs for your business.
With AGVs, businesses can reduce the need for additional workers and avoid the costs of finding and training new personnel. According to the Bureau of Labor Statistics (BLS), workers’ salaries increased by 1.2% while benefit costs increased by 1.8%. It’s important to note that every year, salaries and benefits tend to go up as employees gain more experience. It can increase labor costs, but with AGVs, businesses can keep costs low and improve their bottom line. AGVs can even operate fixed systems, like conveyors.
However, it’s important to note that fixed automation systems can be expensive and sometimes slow the workflow. Sometimes, AGV robots can stop another facility’s operation. And it results in reduced production. However, unlike fixed automation systems, AGVs can be reprogrammed for new tasks and upgraded for better capabilities.