Collaborative Robots in Manufacturing: Boosting Efficiency and Safety
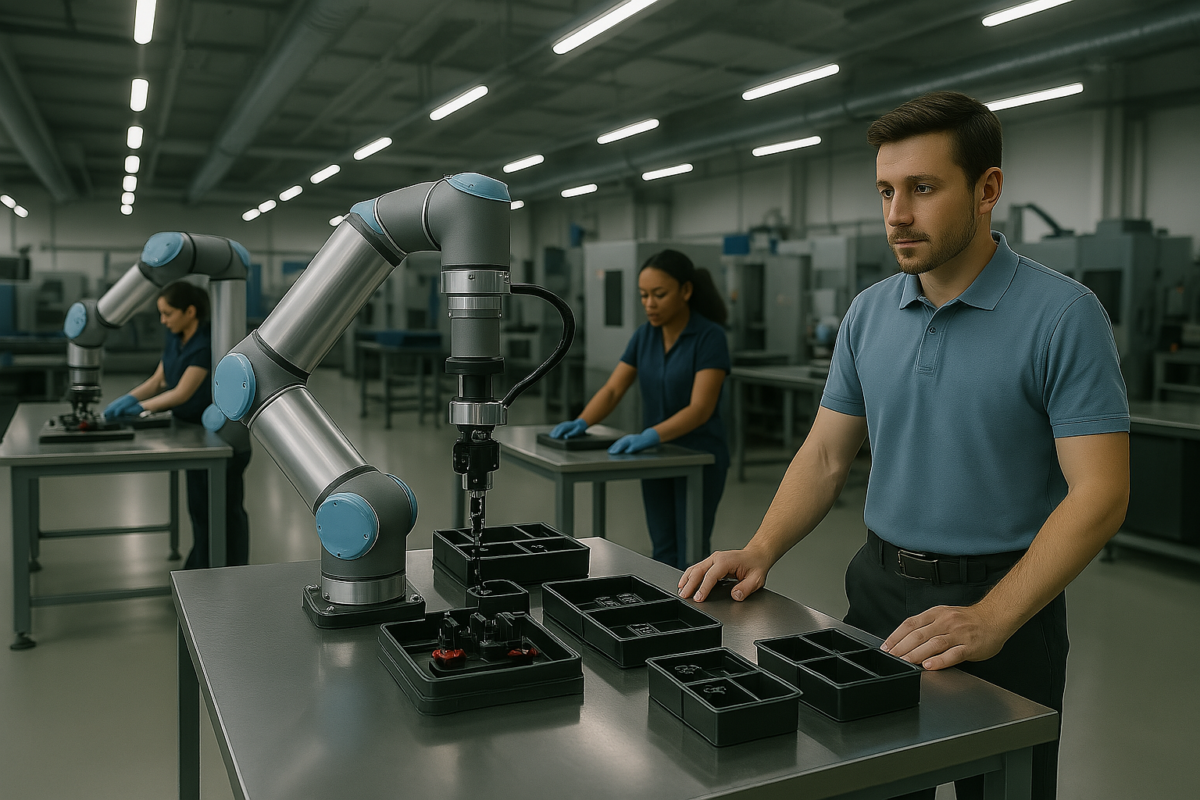
Introduction
Manufacturing is changing fast. Factories are moving from rigid, isolated machines to smart, adaptive systems. At the heart of this shift are collaborative robots, or cobots. These robots are designed to work safely alongside humans, combining automation with flexibility. As a result, collaborative robots in manufacturing are helping companies boost productivity, cut downtime, and create safer workplaces, all at once.
What Are Collaborative Robots?
Collaborative robots are lightweight, sensor-equipped machines built to share workspaces with humans. Unlike traditional industrial robots, which require cages and safety zones, cobots can operate side by side with workers.
Several features set cobots apart:
- Built-in force sensors to detect and respond to contact
- Easy programming with hand-guided teaching
- Adaptive behavior that fits dynamic environments
- Lower upfront cost and space requirements
Because they are safe and easy to deploy, cobots are ideal for small and mid-sized manufacturers looking to embrace automation without major infrastructure changes.
How Cobots Are Revolutionizing Manufacturing Floors
Manufacturers across sectors, from automotive to electronics, are deploying cobots to handle repetitive or dangerous tasks. This allows human workers to focus on higher-value responsibilities like quality control or system monitoring.
Here’s how cobots improve operations:
1. Enhanced Productivity
Cobots work consistently and without fatigue. They help reduce cycle times by handling tasks like:
- Assembly line automation
- Material loading and unloading
- Machine tending
- Packaging and palletizing
As productivity increases, manufacturers can scale operations without scaling headcount.
2. Improved Safety
Workplace injuries cost billions each year. Cobots are built to minimize accidents. Features like force limitation and collision detection ensure they stop or slow down when encountering resistance.
Instead of replacing humans, cobots reduce their exposure to:
- Sharp tools or hot surfaces
- Repetitive strain from lifting
- Enclosed or hazardous environments
In this way, cobots create a safer, more ergonomic workplace.
3. Workforce Augmentation, Not Replacement
A major fear with robotics is job loss. Cobots, however, are designed to augment human skills, not replace them. While robots take over monotonous jobs, workers can:
- Oversee multiple cobots at once
- Train and program robots for new tasks
- Move into creative or supervisory roles
This partnership model boosts job satisfaction and opens up new career paths in robotics and automation.
Also Read
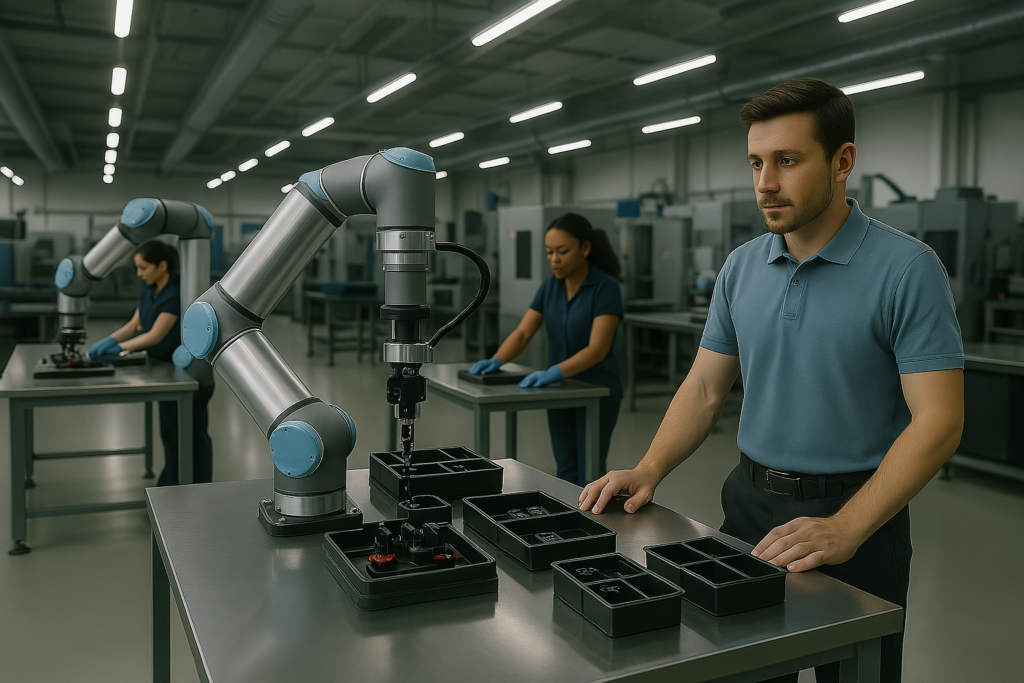
Cobots vs Traditional Industrial Robots
While both types automate tasks, their design and purpose differ significantly:
Feature | Collaborative Robots | Traditional Robots |
---|---|---|
Safety | Built-in, human-safe | Needs cages/barriers |
Setup | Plug-and-play | Complex, costly installation |
Flexibility | Easily reprogrammed | Fixed, rigid tasks |
Cost | Affordable | High upfront investment |
Ideal For | Mixed environments | Isolated operations |
Because of these differences, cobots offer better ROI in dynamic, small-batch manufacturing setups.
Key Industries Benefiting from Cobots
Collaborative robots are finding use in several sectors:
- Automotive: Assisting in interior assembly and inspection
- Electronics: Handling delicate components during PCB assembly
- Pharma: Aiding in lab automation and sterile packaging
- Food and Beverage: Automating packing, sorting, and quality checks
- Metal Fabrication: Supporting welding, deburring, and part polishing
The flexible nature of cobots makes them highly adaptable across these diverse industries.
AI Image Prompt #2
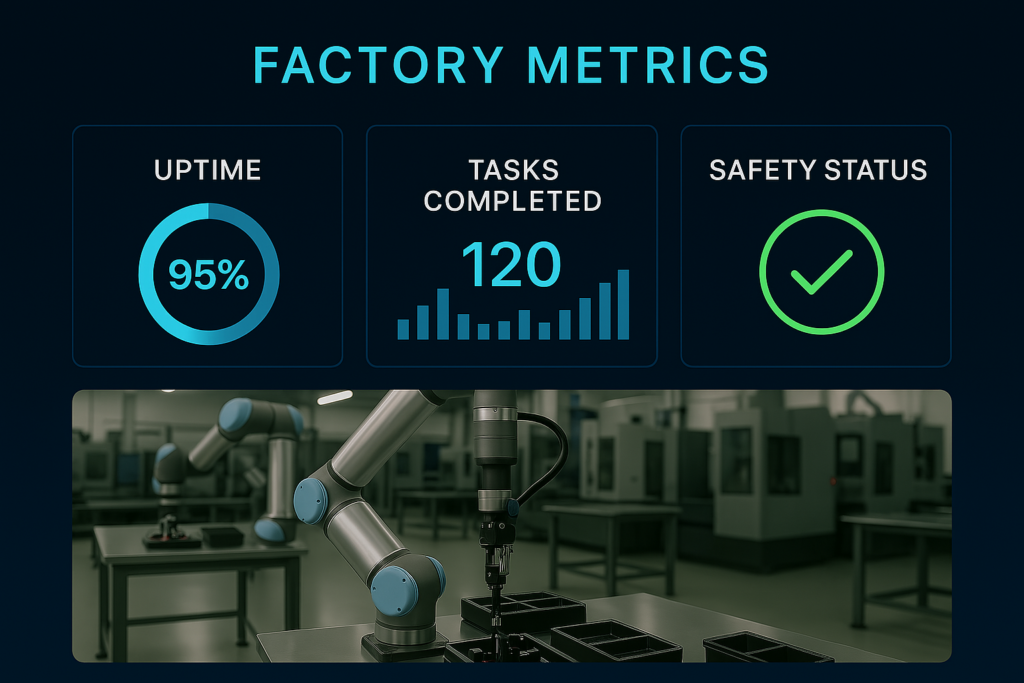
Integration with Smart Manufacturing Systems
Collaborative robots don’t work in isolation. They often integrate with other technologies such as:
- Vision systems for object detection and alignment
- AI algorithms that improve task precision and efficiency
- IoT sensors that monitor temperature, pressure, and movement
- Digital twins for simulating and optimizing workflows before deployment
These integrations enable real-time decision-making and predictive maintenance, further improving factory performance.
Challenges in Cobot Adoption
Despite their benefits, companies may face hurdles when adopting collaborative robots:
- Training requirements for programming and maintenance
- Integration complexity with legacy systems
- Initial cultural resistance from workers unfamiliar with automation
- Choosing the right use case for ROI demonstration
However, most of these challenges are temporary. With proper onboarding and change management, businesses can unlock full value from cobots quickly.
What’s Next for Collaborative Robots?
The future of collaborative robots in manufacturing looks promising. We can expect:
- Smarter AI-powered cobots that learn tasks on the fly
- Industry-specific models tailored for precision or heavy-duty work
- Cloud-connected cobots for global monitoring and updates
- Greater adoption in low-tech industries previously untouched by automation
Eventually, cobots will become standard factory assistants, just like forklifts or conveyor belts once did.
Conclusion
Collaborative robots in manufacturing are more than a trend. They represent a shift toward safer, smarter, and more efficient production. As factories evolve, cobots will be critical in creating environments where people and machines thrive together.
Ready to Explore More?
🎯 Want to integrate collaborative robots into your facility? Download our Cobot Deployment Checklist to assess readiness, cost, and best-fit applications.