How Predictive Maintenance Improves Robotic Picker Lifespan
The warehouse automation market size is at around $29 billion in 2025 and is projected to grow to $63 billion by 2030. At the heart of these massive operations are robotic pickers. They are essential tools that speed up processes, cut down on labor costs, and get orders out the door with incredible accuracy. But even the best machines have a weak spot: they wear out. Traditional maintenance methods, like waiting for a robot to break down or fixing it on a strict schedule, just can’t keep up with the demands of today’s supply chains. That’s where predictive maintenance AI comes in.
Instead of just reacting to problems, this technology allows warehouses to anticipate them. By constantly analyzing data from robot sensors and using machine learning, AI tools can predict when a picker might fail. This not only extends the robot’s lifespan and prevents expensive downtime, but it also ensures that the supply chain keeps moving smoothly, without any sudden interruptions.
In this article, we’ll dive into how this powerful technology works, why it’s so important for keeping warehouse robots in peak condition, and what the future holds for the reliability of these tireless machines.
What Is Predictive Maintenance in Robotics?
Predictive maintenance is the use of data-driven tools to forecast when a machine will need servicing. Unlike scheduled maintenance, which assumes all machines wear down at the same rate, predictive systems rely on real-time insights.
Every robotic picker, from its motors to its grippers, generates a constant stream of operational data. This data is the digital footprint of a machine’s physical state. AI hardware management systems collect this data from a variety of sensors:
Vibration Sensors: A robot’s motor and joints vibrate in a consistent pattern. Changes in this pattern, such as increased amplitude or new frequencies, can signal a misaligned bearing or a worn gear.
Temperature Sensors: Overheating in a motor, battery, or circuit board is a classic sign of impending failure. AI models can detect subtle temperature increases that a human would miss.
Acoustic Sensors: The sound a robot makes is a rich source of information. A new grinding noise or a change in pitch can indicate a lubrication issue or a loose component.
Current and Voltage Sensors: Spikes or drops in electrical usage can indicate a failing motor or a short circuit. Operational Data: The system also tracks key performance indicators like cycle times, force applied by grippers, and distance traveled.
A robot failure prediction model ingests this data, analyzes it against historical trends, and identifies the subtle, early warning signs of a component’s degradation. As a result, it allows the system to transition from a static maintenance schedule to a dynamic, condition-based one
Also See: Why Sensor Fusion Is the Future of Robotic Picking Accuracy
Why Robotic Picker Maintenance Matters
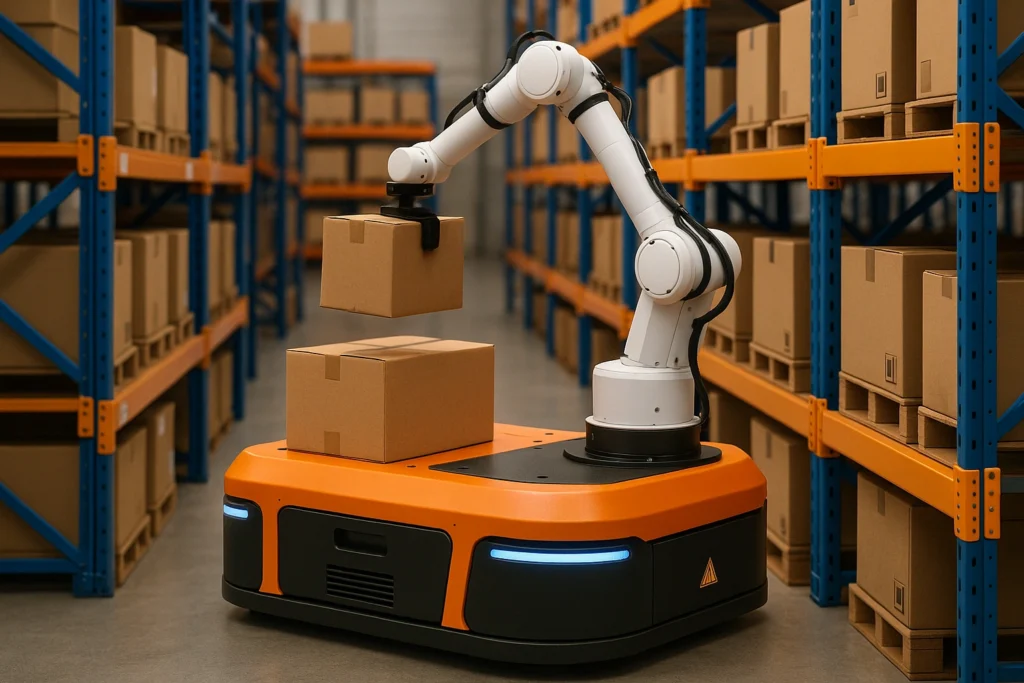
A robotic picker breakdown doesn’t just stop one task. It can disrupt entire operations. The risks of ignoring robotic picker maintenance include:
Downtime costs: Every hour offline means delayed shipments.
High repair expenses: Emergency fixes are always more expensive than preventive care.
Shorter robot lifespan: Constant breakdowns reduce long-term value.
Safety risks: A malfunctioning robot can damage goods or pose risks to workers.
With predictive tools, these risks shrink dramatically. Maintenance becomes proactive instead of reactive, making warehouses more resilient.
How Predictive Maintenance Works for Robotic Picker Maintenance
Predictive maintenance AI combines multiple layers of technology. Here’s how it functions step by step:
1. Data Collection from Smart Picker Systems
Robotic pickers come loaded with sensors. These track vibration, temperature, torque, and power usage. Over time, small changes in these values indicate potential wear and tear.
2. Machine Learning Models
AI algorithms analyze the data. They detect patterns that humans might miss—for example, a slight increase in motor heat that signals early stress.
3. Condition Monitoring
The system continuously checks the health of every robot. If it notices unusual behavior, alerts are generated.
4. Maintenance Scheduling
Instead of random downtime, robots are serviced exactly when they need it. Parts are replaced before failure, keeping the machine running longer.
5. Feedback Loops
Each repair feeds back into the system. The AI becomes smarter, making robot lifecycle tools more accurate over time.
Benefits of Predictive Maintenance for Robotic Pickers
The benefits of predictive maintenance go far beyond just preventing breakdowns. It is a powerful robot lifecycle tool that maximizes return on investment.
Extended Component Lifespan
Instead of replacing a part at 80% of its potential life (as is often the case with preventive maintenance), predictive systems allow it to be used to 95% of its potential. This reduces waste and cuts down on part replacement costs.
Optimized Resource Allocation
Maintenance teams can focus their efforts on robots that actually need attention. They are no longer performing unnecessary checks on healthy machines, freeing up labor for other critical tasks.
Improved Safety
A failing component can be a safety hazard. By identifying and addressing issues before they escalate, predictive maintenance enhances the overall safety of the warehouse environment.
Maximized Warehouse Uptime
This is perhaps the most significant benefit. By eliminating unscheduled downtime, a business can ensure its operations run at peak efficiency, meeting order fulfillment targets and enhancing customer satisfaction. Accordingly, it translates directly to bottom-line results.
Key Predictive Maintenance Tools for Robotic Pickers
1. Vibration Sensors
Subtle vibration changes often reveal motor or joint issues. These sensors act as the first warning system.
2. Thermal Cameras
Heat signatures show when motors, processors, or batteries are under stress.
3. Current and Voltage Monitors
Tracking energy flow ensures power systems remain stable and prevents unexpected shutdowns.
4. AI-Driven Dashboards
Centralized platforms allow managers to monitor robot health across the warehouse in real time.
5. Cloud-Based Data Storage
Large datasets of robot performance are stored and analyzed, giving insights into fleet-wide behavior.
Case Applications in Warehouse Robotics
High-Volume E-Commerce Warehouses
Robots work nonstop in these facilities. Predictive maintenance ensures machines keep up with intense order demand.
Cold Storage Logistics
Extreme temperatures can stress robotic systems. Predictive tools detect early wear from cold environments.
Automated Distribution Centers
With thousands of robots in motion, predictive maintenance prevents system-wide shutdowns.
Retail Supply Chains
In seasonal peaks, robots must operate without fail. Predictive monitoring ensures readiness for high-demand periods.
Challenges of Predictive Maintenance in Robotics
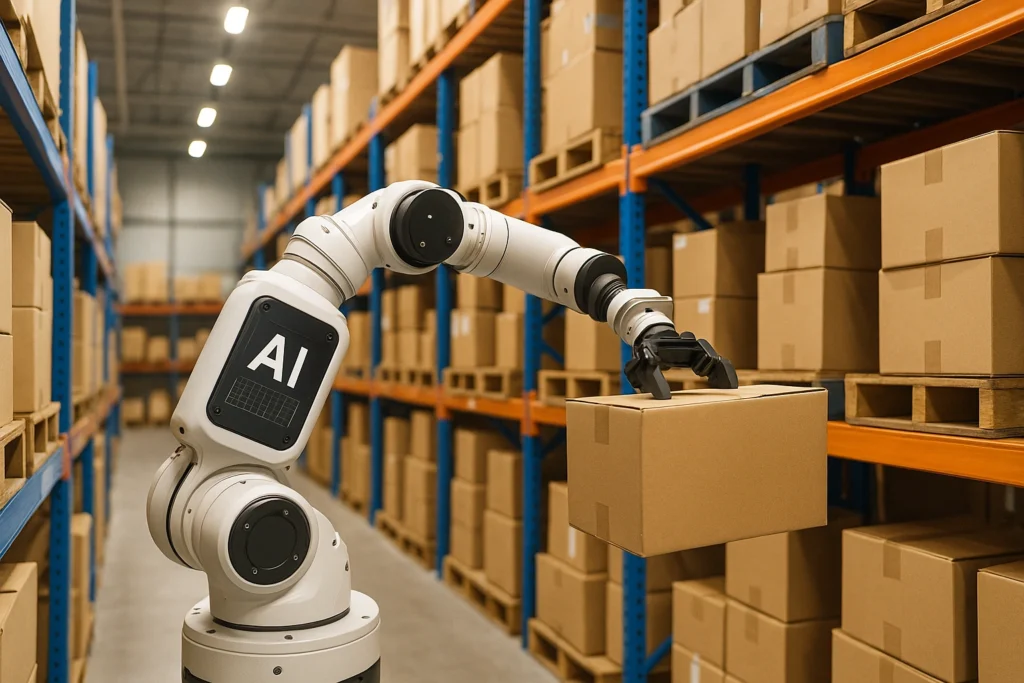
Adopting predictive maintenance is not without hurdles like:
- High Initial Investment: Installing sensors and AI systems requires upfront costs.
- Complex Data Streams: Multiple robots produce huge amounts of data that must be processed.
- Integration Issues: Predictive tools must connect with existing warehouse management software.
- Skill Gaps: Teams must be trained to interpret and act on predictive insights.
Overcoming these challenges requires careful planning, vendor partnerships, and investment in long-term infrastructure.
Also See: Cobots vs Robots: What’s Shaping the Future of Work?
The Future of Robotic Picker Predictive Maintenance
The integration of predictive maintenance AI is the next major leap in warehouse automation. As robot fleets grow in size and complexity, the need for intelligent, automated care will become even more critical. Companies that embrace this technology will gain a significant competitive advantage through lower operational costs, higher efficiency, and a more resilient supply chain.
The era of “set it and forget it” robotic systems is over. The future belongs to smart picker systems that not only perform their tasks flawlessly but also communicate their health, predict their needs, and effectively manage their own lifecycle. This synergy between robotics and AI is the key to unlocking the full potential of automation and building a more robust and reliable future.
FAQ: Robotic Picker Maintenance
How does predictive maintenance differ from preventive maintenance?
Preventive maintenance follows a fixed schedule. Predictive maintenance uses AI to monitor real-time data and intervene only when necessary.
Can predictive maintenance completely eliminate robot failures?
Not entirely. But it greatly reduces the frequency and severity of failures.
What tools are needed for predictive maintenance in warehouses?
Vibration sensors, thermal monitors, AI dashboards, and cloud analytics platforms.
Is predictive maintenance affordable for small warehouses?
While initial costs are high, the savings from reduced downtime and longer robot life often outweigh the expense.
Conclusion
With tools that predict failures, manage robot lifecycles, and create smart picking systems, warehouses become more resilient and efficient, which is crucial in today’s competitive market.
Looking ahead, we can expect to see things like self-healing robots, connected fleets, and maintenance strategies that are completely data-driven. Ultimately, predictive maintenance isn’t just a nice-to-have anymore. It’s the core of building reliable, future-proof warehouse automation.